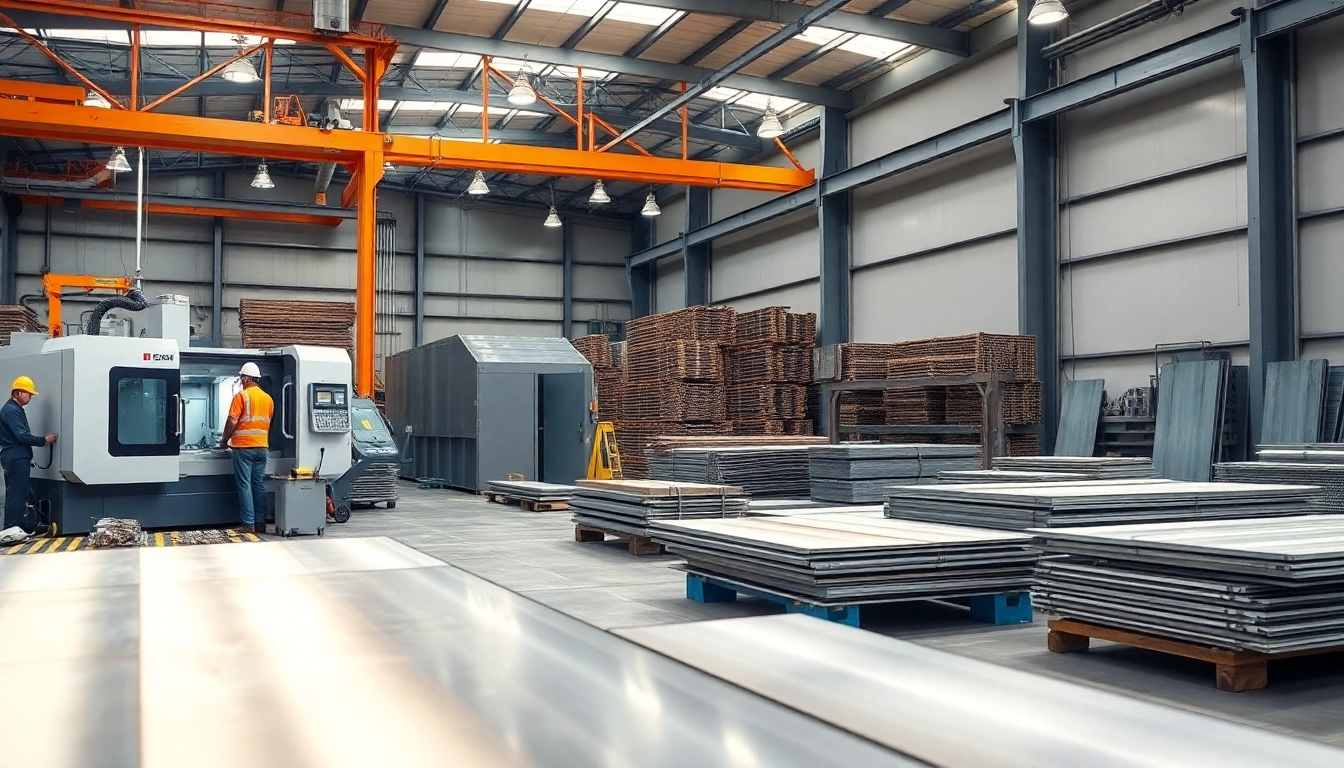
Understanding Metal Manufacturing in Edmonton
The metal manufacturing industry in Edmonton plays a vital role in driving innovation, supporting local businesses, and contributing to the province’s economy. With a rich history and a network of skilled professionals, the sector continues to evolve through advancements in technology and methodologies. As organizations seek high-quality metal products, understanding the nuances of this industry becomes imperative. One key player in this field is metal manufacturer edmonton, which exemplifies quality and precision in its offerings.
Overview of the Metal Industry
The metal industry encompasses a myriad of activities, from the extraction of raw materials to the fabrication and finishing of metal products. In Edmonton, various types of metals such as aluminum, steel, and copper are processed to fulfill diverse market needs. As an integral part of the supply chain, metal manufacturing supports numerous sectors, including construction, automotive, aerospace, and energy. With global trends pointing toward sustainability and efficiency, Edmonton’s metal manufacturers are increasingly adopting innovative practices that not only comply with environmental standards but also enhance productivity.
Key Players in Edmonton’s Metal Manufacturing
Edmonton is home to several notable metal manufacturers who contribute significantly to the local economy. Companies such as XYZ Metalworks and ABC Fabricators are among the key players, each specializing in different aspects of metal processing and fabrication. These organizations leverage their expertise to provide customized solutions, catering to the unique demands of clients across various industries. Networking within trade associations and participating in exhibitions has enabled these manufacturers to build a strong presence, both locally and nationally.
Innovations Impacting the Sector
In recent years, advancements in technology have drastically changed the landscape of metal manufacturing. Innovations such as automation, 3D printing, and smart manufacturing are reshaping operational workflows, enhancing quality control, and reducing lead times. For instance, the integration of robotics in machining processes allows for precision that was previously unattainable and facilitates workforce safety by minimizing human exposure to hazardous environments. Additionally, the adaptation of eco-friendly practices, including recycling and energy-efficient production methods, demonstrates the sector’s commitment to sustainability and long-term growth.
Quality Standards in Metal Manufacturing
Quality assurance in metal manufacturing is paramount. In a competitive landscape, delivering products that meet or exceed customer expectations is essential for maintaining a good reputation. Several standardized regulations and certifications guide manufacturers in ensuring product quality and compliance.
Importance of Certifications
Certifications such as ISO 9001, AS9100, and API specifications serve as benchmarks to demonstrate a manufacturer’s commitment to quality and continuous improvement. Obtaining these certifications not only enhances credibility but also opens up opportunities for participation in multinational projects and contracts. Edmonton’s metal manufacturers are increasingly pursuing these certifications to align their processes with international standards, increasing their competitiveness on a global scale.
Meeting Customer Specifications
Tailoring products to meet specific customer needs is a cornerstone of successful metal manufacturing. This requires effective communication channels between manufacturers and their clients to understand performance requirements, material preferences, and dimensions. By implementing customer feedback mechanisms and engaging in collaborative design processes, manufacturers can develop solutions that precisely match customer specifications, ultimately leading to stronger business relationships and repeat business.
Quality Control Processes
A robust quality control system is instrumental in identifying defects before products reach the market. Techniques such as Six Sigma and Lean Manufacturing are increasingly adopted to optimize workflows, minimize waste, and streamline processes. Routine inspections, testing, and documentation are essential components of a comprehensive quality management system. Additionally, utilizing technology such as data analytics can help identify patterns and potential issues, allowing for proactive measures to enhance quality assurance.
The Manufacturing Process Explained
Understanding the intricacies of the manufacturing process is key to appreciating the craftsmanship involved in metal fabrication. This process comprises multiple stages, starting from raw material selection and culminating in the final treatment and finishing stages.
Raw Material Selection
The choice of raw materials lays the foundation for the quality of the finished product. Factors such as tensile strength, corrosion resistance, and thermal properties are crucial considerations that impact the overall performance of metal components. In Edmonton, local manufacturers often have access to a wide variety of metals, allowing them to select the most suitable materials tailored to specific applications. Engaging with trustworthy suppliers who guarantee quality and sustainability in their raw materials ensures the integrity of the manufacturing process.
Machining Techniques Used
Once raw materials are selected, various machining techniques come into play. Common processes used in Edmonton’s metal manufacturers include CNC machining, milling, turning, and laser cutting. Each technique has its advantages, and the choice largely depends on the desired precision, volume, and complexity of the parts being produced. CNC machining, for example, offers high accuracy and repeatability, making it ideal for producing intricate components. Manufacturers are continually investing in the latest technologies to improve efficiency and minimize waste during machining operations.
Finishing and Treatment Methods
After machining, the finishing stage involves surface treatments that enhance the durability and aesthetic appeal of the metal products. Techniques such as coating, anodizing, and polishing are employed to achieve specific characteristics, such as corrosion resistance or improved surface finish. Understanding these finishing processes is vital for manufacturers to provide products that not only meet functional requirements but also appeal visually to customers, thereby influencing purchasing decisions.
Challenges Faced by Metal Manufacturers
While the metal manufacturing industry is thriving in Edmonton, it is not without challenges. From supply chain disruptions to managing costs, manufacturers must navigate various factors that can impact their operations.
Supply Chain Management Issues
Supply chain management is a critical aspect of metal manufacturing. Fluctuations in raw material prices, limited availability of specific metals, and transportation disruptions can all hinder production schedules and inflate costs. Consequently, manufacturers must develop strong relationships with multiple suppliers, maintain transparency throughout the supply chain, and implement inventory management systems to mitigate risks associated with supply disruptions. Investing in local suppliers can enhance resilience while supporting the local economy.
Cost Control in Production
Maintaining cost-effectiveness is essential for profitability, especially in a competitive marketplace. Manufacturers are tasked with optimizing production methods while controlling overhead costs. Implementing lean manufacturing principles, automating repetitive tasks, and utilizing data analytics can help identify areas of inefficiency and drive cost reduction efforts. Additionally, conducting regular financial analyses can provide insights into resource allocation and overall production costs, guiding future decision-making.
Adapting to Market Demand Changes
Market demand for metal products can be volatile, influenced by shifts in industries such as construction, automotive, and consumer goods. Staying ahead of these changes requires agility in production capabilities and the ability to pivot quickly to meet emerging trends. Manufacturers in Edmonton are increasingly adopting flexible manufacturing systems that allow them to alter production schedules and outputs based on real-time market intelligence. Continuous monitoring of market conditions, along with customer feedback, can provide valuable insights for strategic planning.
Choosing the Right Metal Manufacturer in Edmonton
For companies seeking metal manufacturing services, selecting the right partner is critical to ensuring quality and meeting project timelines. Evaluating various factors can help in making an informed decision.
Factors to Consider When Selecting a Manufacturer
When choosing a metal manufacturer, several factors should be taken into account, including industry experience, production capabilities, and technology adoption. A manufacturer with a proven track record in a relevant industry can bring valuable expertise to complex projects. Additionally, it is essential to assess the scalability of their operations and whether they can handle the volume and complexity of your requirements.
Evaluating Manufacturer Capabilities
Potential clients should request information about a manufacturer’s certifications, tooling, and machinery capabilities. Visiting the facility can provide insights into their operational practices, quality control systems, and workforce competencies. Understanding their capacity to innovate and adapt to evolving market demands can further indicate their potential as a reliable manufacturing partner.
Customer Testimonials and Case Studies
Word-of-mouth recommendations and testimonials can significantly influence the choice of a metal manufacturer. Reviewing case studies and customer feedback can shed light on a manufacturer’s ability to deliver on promises, manage timelines, and address potential project challenges effectively. Engaging with existing clients through conversations can provide further assurance regarding their satisfaction and the manufacturer’s reliability.