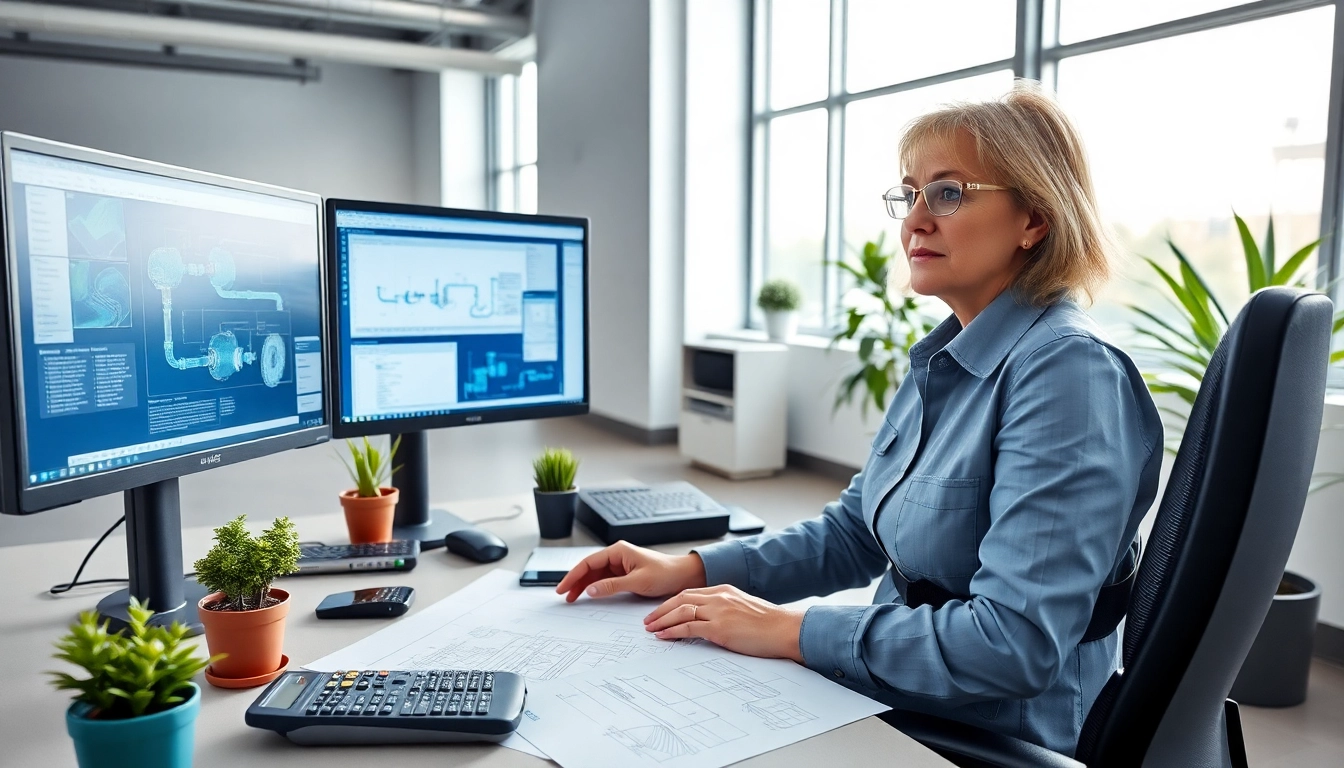
Understanding Piping Stress Analysis
What is Piping Stress Analysis?
Piping stress analysis is a critical engineering process that aims to ensure the structural integrity and operational performance of piping systems by evaluating the stresses, strains, and deformations due to different operating conditions. This analysis involves applying mechanical engineering principles and tools to assess how various factors—such as temperature, pressure, and fluid flow—impact the piping system. By numerically modeling these conditions, engineers can predict how piping will react under various service scenarios, enabling them to mitigate potential failures and optimize designs.
Importance in Engineering Projects
The significance of piping stress analysis in engineering projects cannot be overstated. As pipes transport fluids in a myriad of industries—from oil and gas to chemical processing—understanding the potential stresses they face is essential for enhancing safety, reliability, and efficiency. Effective stress analysis helps identify critical failure points before they become a problem, minimizes downtime due to repairs, and ensures compliance with industry standards. Furthermore, thorough analysis contributes to the overall project timeline and cost management, making it an indispensable aspect of engineering consultancy. Companies often turn to a piping stress analysis company for expert solutions and insights to navigate these complexities.
Common Techniques and Tools
Several techniques and tools are employed in piping stress analysis, including:
- Theoretical Analysis: Utilizes mathematical models to predict stress and strain in piping systems.
- Finite Element Analysis (FEA): A numerical method that divides structures into smaller elements to analyze complex behaviors under various conditions.
- Computational Fluid Dynamics (CFD): Simulates fluid flow and its interaction with pipe walls to assess thermal and pressure scenarios.
- Software Tools: Applications such as CAESAR II, ANSYS, and AutoPIPE are extensively used to facilitate simulations and visualizations of stress analyses.
Key Challenges Faced by Piping Stress Analysis Companies
Identifying Stress Points and Risks
One of the foremost challenges in piping stress analysis is accurately identifying stress points and potential risks. Given the complexity of modern piping systems, with their intricate configurations and the variety of materials used, engineers must navigate a labyrinth of factors that could contribute to stress accumulation. Critical stress points often arise at joints, bends, or supports, underlining the importance of meticulous modeling and real-time data integration to avoid underestimations. Failure to recognize these vulnerabilities can lead to catastrophic failures, resulting in not only financial losses but also severe safety risks.
Compliance with Industry Standards
Adhering to industry standards is another significant challenge. Various organizations, including ASME (American Society of Mechanical Engineers) and API (American Petroleum Institute), set stringent guidelines for piping systems’ design and operational parameters. Not only must piping stress analysis companies maintain compliance with these standards, but they also need to stay updated on regional regulations and codes, which can vary significantly. Non-compliance can result in legal ramifications, project delays, or costly rework. Therefore, a comprehensive understanding of current industry regulations is vital for engineering firms undertaking piping stress analysis.
Integrating Advanced Software Solutions
The rapid evolution of technology presents both opportunities and challenges for piping stress analysis companies, especially regarding software integration. Advanced software solutions can dramatically enhance the accuracy and efficiency of analyses. However, the integration process is often fraught with difficulties, including training personnel, ensuring interoperability between software systems, and maintaining data integrity. Companies must invest in proper training and resources to leverage these tools effectively, which can be a significant barrier for smaller firms with limited budgets.
Best Practices for Effective Piping Stress Analysis
Leveraging Innovative Technology
To achieve effective piping stress analysis, leveraging innovative technology is vital. Using advanced simulation software allows for better predictive modeling and real-time scenario analysis, addressing common stress challenges more dynamically. Techniques such as virtual reality (VR) and augmented reality (AR) can also enhance design visualization, leading to more informed decision-making in the design phase. Regularly updating technology infrastructures and staying current with software releases can elevate an engineering company’s analytical capabilities significantly.
Monitoring and Maintenance Strategies
Post-analysis monitoring and maintenance strategies are fundamental to sustaining piping system integrity. Installing sensors to collect real-time data on pressure, temperature, and flow can provide ongoing insights into system performance. This data enables companies to perform predictive maintenance, addressing issues before they escalate into failures. Regular inspections and routine assessments are crucial components of a holistic approach to piping stress management, ensuring long-term reliability.
Creating Comprehensive Documentation
A detailed documentation process is essential for effective piping stress analysis. Comprehensive records not only provide a transparent view of the analysis process and results but also serve as a resource for future maintenance and upgrades. Documentation should include stress reports, compliance checks, and any alterations made during the project lifecycle. Additionally, it facilitates knowledge transfer between engineering teams and helps in audits, ensuring that organizations meet regulatory requirements while enhancing internal processes.
Case Studies: Success Stories in Piping Stress Analysis
Project Overview and Objectives
Case studies illustrate the successful application of piping stress analysis in real-world scenarios. One notable project was for an offshore oil platform, where the objective was to design a new piping system that had to withstand severe environmental conditions, including high winds and dynamic loads. The engineering team aimed to maximize the safety and efficacy of the proposed systems while ensuring full compliance with industry standards.
Methodologies Applied
The team employed a combination of FEA and CFD to analyze stress distributions and thermal effects in the new piping layout. These methodologies allowed them to visualize potential stress points and adjust the designs accordingly. Additionally, they integrated smart monitoring technologies to provide ongoing oversight post-installation. This combination of methods ensured a robust system design that accounted for both external and internal pressures.
Results and Key Takeaways
The outcomes were significantly positive; the project not only met all safety standards but also resulted in a 20% reduction in material costs thanks to optimized design choices. The case study emphasized the importance of thorough analysis and modeling in achieving effective engineering solutions, reinforcing that proactive measures in stress analysis not only enhance safety but can also lead to substantial cost savings and efficiencies in project execution.
Future Trends in Piping Stress Analysis
Emerging Technologies and Their Impact
The future of piping stress analysis is set to be revolutionized by emerging technologies. Innovations such as machine learning and artificial intelligence are increasingly being utilized to optimize design processes by predicting stress responses under various conditions. These technologies enable more adaptive and responsive engineering philosophies, allowing for real-time adjustments and decision-making. Furthermore, advanced materials, like composites and lightweight structures, are gaining traction to enhance durability while reducing stress loads significantly.
The Shift Towards Automation
Another significant trend is the shift towards automation within the stress-analysis workflow. As technology evolves, tasks that were once manual are being automated to improve efficiency and reduce human error. Automated stress calculation tools and reporting systems reduce time spent on repetitive tasks and allow engineers to focus their efforts on higher-value analysis and design optimization processes.
Preparing for Industry Changes
As the industry continues to evolve, piping stress analysis companies must be agile and adapt swiftly to changes. This includes embracing new regulations, sustainable practices, and client demands for faster and more economical solutions. Training staff on emerging technologies and adopting a forward-thinking mindset will be critical for companies to maintain competitive advantages in this dynamic environment. Staying proactive about learning and development will ensure that these organizations remain at the forefront of the industry, equipped to tackle the complexities of modern piping system design.