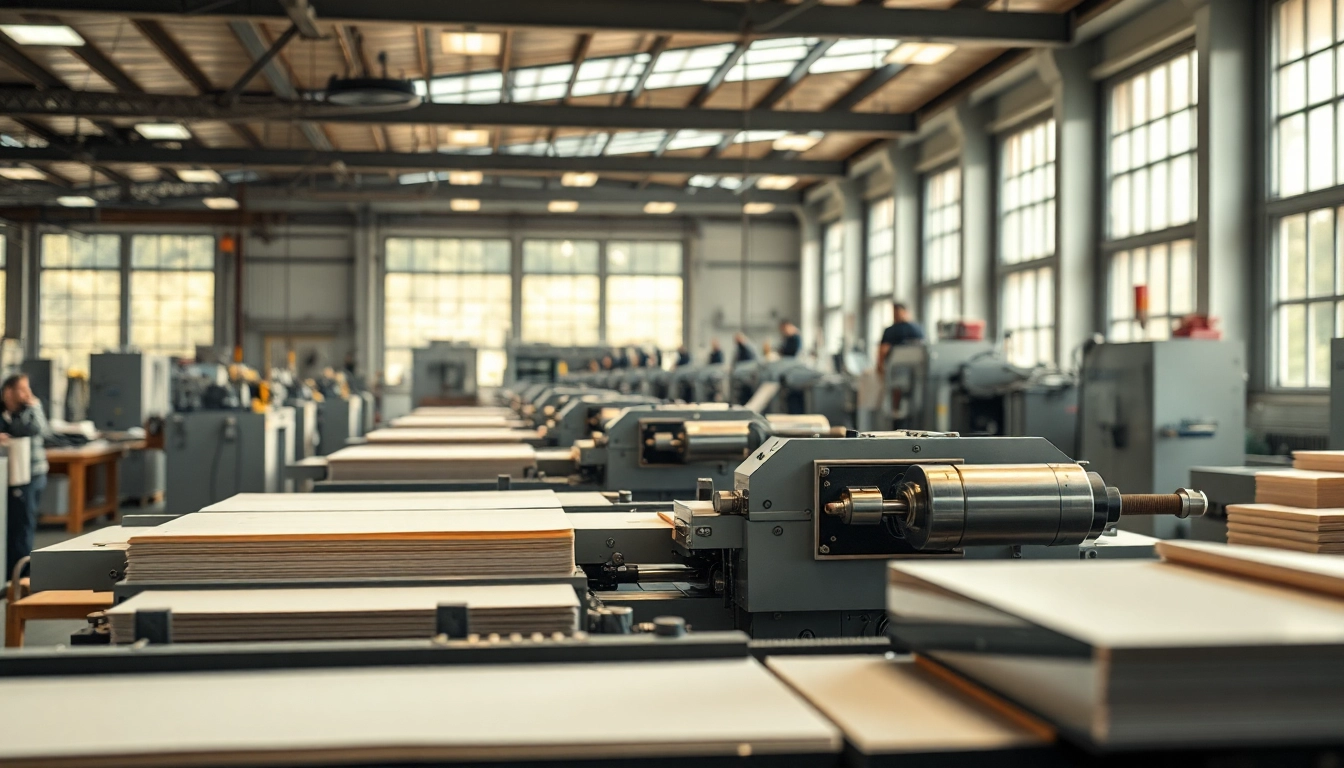
Understanding Precision Die Cutting
What is Precision Die Cutting?
Precision die cutting is a manufacturing process that involves cutting materials with a high degree of accuracy to produce specific shapes or components. This technique utilizes a die, which is essentially a specialized tool, to create custom cut parts from sheets or rolls of material. It is an essential step in many industrial applications, particularly where precision and efficiency are paramount.
The die cutting process can be employed with various materials, including paper, plastic, metal, and foam. Industries that benefit from precision die cutting include packaging, automotive, electronics, medical devices, and more. With its ability to create intricate designs with minimal waste and optimal speed, precision die cutting has become a go-to solution for manufacturers looking to streamline their production processes.
How Precision Die Cutting Works
The precision die cutting process begins with the design of the die itself. This can be made from various materials, including steel or other robust metals, tailored specifically for the task at hand. Once the die is created, the manufacturing process involves placing the material to be cut in the machine, which then presses the die onto the material with substantial force, thereby cutting it into the desired shape.
There are two primary types of die cutting systems used in precision applications: flatbed and rotary die cutting. Flatbed die cutting utilizes a stationary die and moves the material beneath it, while rotary die cutting employs a cylindrical die that rolls over a material feed, allowing for rapid, continuous production and minimizing downtime.
Innovative technologies have further enhanced the process, with the integration of computer controls that allow for real-time adjustments and optimizations, leading to finer tolerances and a higher quality finish.
Applications of Precision Die Cutting
Precision die cutting serves a multitude of industries and applications. Some common applications include:
- Packaging: Custom boxes, blister packs, labels, and other packaging materials require precise cuts to ensure product fit and protection.
- Automotive Parts: Durable components such as gaskets, seals, and insulation require precision to meet stringent industry standards.
- Electronics: Battery management systems and circuit boards benefit from precise cutouts in protective casings.
- Medical Devices: Devices such as surgical instruments and wearables utilize precision die cutting for intricate components and assemblies.
- Textiles: Fashion and upholstery fabrics can be die-cut into specific patterns for consistent production.
Benefits of Precision Die Cutting
Cost-Effectiveness in Production
One significant advantage of precision die cutting is its cost-effectiveness, especially in large-volume production. By achieving a higher yield from raw materials due to accurate cuts, companies can significantly reduce waste. Furthermore, automating the process accelerates production speeds, thereby decreasing labor costs and increasing overall production capacity.
Enhancing Material Utilization
Die cutting greatly enhances material utilization, allowing businesses to utilize their raw materials more efficiently. By providing a high degree of precision, die cutting minimizes off-cuts, maximizing usable product per sheet of material. This optimized use of materials contributes to reduced production costs and supports sustainability efforts by lessening waste.
Speed and Efficiency Advantages
A key benefit of employing precision die cutting is the remarkable speed and efficiency it offers. Once the initial setup is complete, producing complex shapes can occur much faster than traditional cutting methods. The high-speed capability of rotary die cutting machines, for instance, enables manufacturers to process thousands of parts in a finite time frame, significantly improving turnaround times and meeting tight deadlines.
Common Challenges in Precision Die Cutting
Dealing with Material Variability
While precision die cutting is advantageous, it does present challenges, particularly regarding material variability. Different materials possess unique characteristics affecting how they behave during the cutting process. Changes in thickness, elasticity, and hardness can influence the die’s performance, requiring continual adjustments to maintain quality.
To mitigate these challenges, it is crucial to perform thorough material testing and adjust the die and machine parameters accordingly. Utilizing advanced software can also help simulate material behavior prior to production, enabling optimized settings.
Quality Control Issues
Ensuring consistent quality is another challenge in precision die cutting. Small variations in die settings, material quality, or machine calibration can lead to defects. Implementing comprehensive quality control protocols, including regular inspections of the dies and monitoring output for discrepancies, can help maintain high standards.
Choosing the Right Equipment
The selection of the appropriate die cutting equipment is essential for achieving desired outcomes. With various die cutting methods, materials, and applications, businesses must conduct detailed assessments to align their equipment choice with their specific production needs. Factors such as budget, volume requirements, specific applications, and ease of maintenance should guide equipment selection.
Best Practices for Precision Die Cutting
Maintenance and Upkeep of Die-Cutting Machines
Regular maintenance of die-cutting machines is imperative to ensure your equipment operates at peak performance. Establish a maintenance schedule that includes cleaning, lubrication, and parts replacement as needed. This proactive approach minimizes unplanned downtime and extends the lifespan of your machines.
Training Staff for Optimal Performance
Investing in comprehensive training programs for machine operators ensures they become proficient in operating die-cutting equipment effectively and safely. Well-trained staff can quickly adapt settings for varying materials and recognize early signs of mechanical issues, preventing production delays and enhancing product quality.
Choosing High-Quality Die Materials
The quality of die materials is crucial for precise cutting and longevity. Opting for high-grade materials not only reduces wear and tear but also enables high precision in repeated use. Partnering with reputable suppliers that understand the specific needs of your applications can enhance the outcomes of your cutting processes.
The Future of Precision Die Cutting
Technological Advancements and Innovations
The die cutting landscape is rapidly evolving due to technological advancements. Innovations such as automated systems, digital die cutting, and feedback-driven controls are enhancing precision and speed significantly. Industries must stay aligned with emerging technologies to maintain their competitive edge and maximize productivity.
Sustainability Practices in Die Cutting
As industries work towards sustainability, precision die cutting is adapting to minimize environmental impacts. Methods such as reducing material waste and energy consumption are gaining traction. Implementing sustainable practices in die cutting not only positions companies as environmentally conscious but also caters to the increasing demand for eco-friendly products.
Market Trends and Customer Demands
The market is witnessing a shift towards more customized and complex designs as consumer preferences evolve. Companies are leaning towards precision die cutting to meet these demands while also maintaining efficiency and cost-effectiveness. Staying abreast of market trends, understanding customer requirements, and adapting to changes will be vital for manufacturers aiming for sustained growth and customer satisfaction.