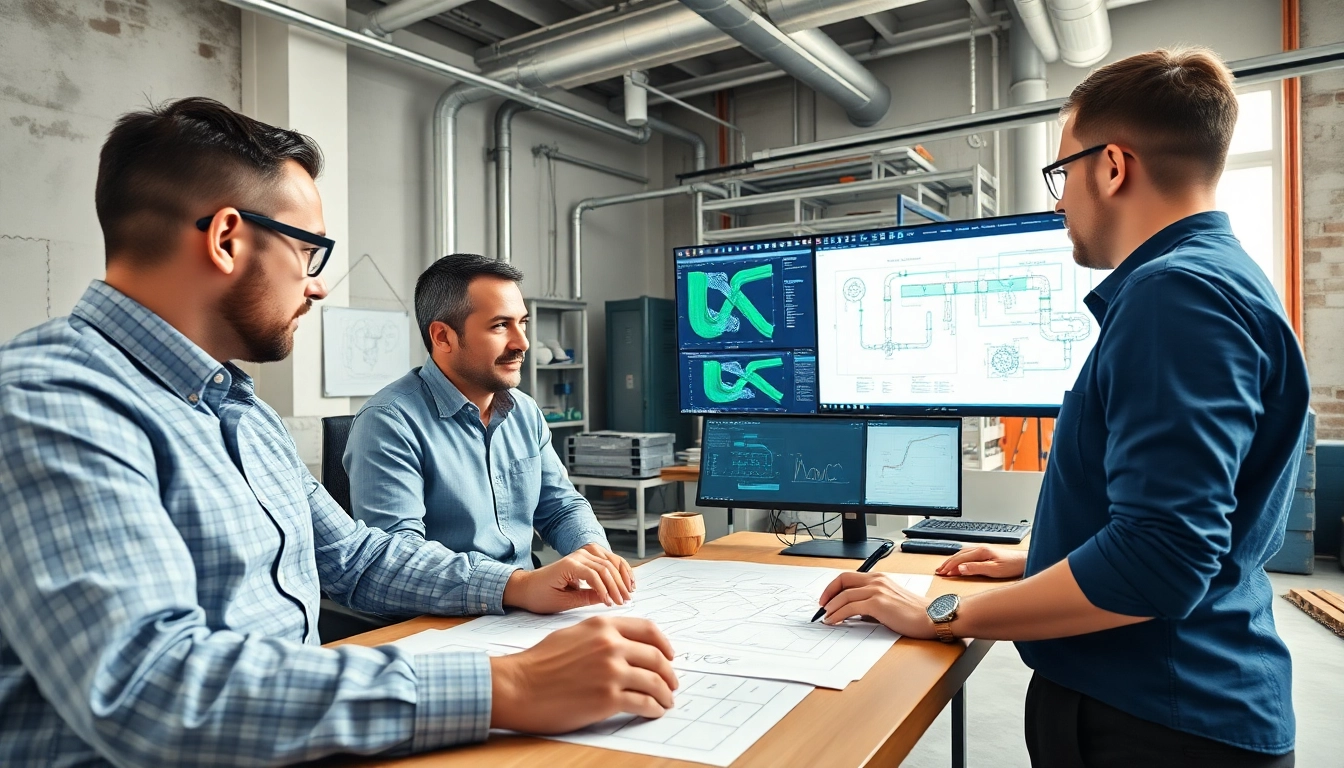
Understanding Piping Stress Analysis
Piping systems play a crucial role in various industries, from oil and gas to power generation, transporting fluids that are essential for operations. One of the key areas of focus when designing and maintaining these systems is piping stress analysis. This analysis ensures that the piping systems are capable of withstanding the various stresses and loads applicable over their service life, enhancing safety and reliability. In this section, we will delve into what piping stress is, the importance of stress analysis, and the factors that influence stress in piping systems.
What is Piping Stress?
Piping stress refers to the internal and external loads experienced by a piping system during its operation. These stresses can arise from several sources, including thermal expansion, pressure variations, and weight loads from the pipes themselves and any fluid within them. When these factors are not adequately accounted for, they can lead to failures or significant operational issues.
There are primarily two types of stresses in piping systems: axial stress and bending stress. Axial stress occurs along the length of the pipe and is mainly due to pressure and thermal expansions. In contrast, bending stress results from changes in the pipe’s layout or support configurations. Understanding these stresses is fundamental to maintaining the integrity and safety of piping systems.
The Importance of Stress Analysis in Piping Systems
Piping stress analysis is essential for several reasons:
- Safety: Proper analysis helps prevent failures that could lead to catastrophic incidents.
- Compliance: Many industries are governed by strict regulations that require adherence to safety standards.
- Operational Efficiency: A well-analyzed piping system operates more efficiently, reducing the risk of unplanned downtime.
- Cost-Effectiveness: Preventing failures can save significant costs associated with repairs, shutdowns, and legal issues.
As industries evolve and standards become more stringent, the need for expert piping stress analysis becomes even more critical.
Key Factors Affecting Piping Stress
Several key factors influence piping stress, including:
- Fluid Properties: The temperature and pressure of the fluid being carried impact the stress distribution within the piping. For instance, higher temperatures can lead to greater thermal expansion.
- Support Configuration: How a pipe is supported can significantly impact the load distribution and stress levels experienced throughout the system.
- Material Properties: Different materials have varying tensile strengths and yield points, meaning that their response to stress will differ depending on the environmental conditions.
- Pipe Size and Thickness: Larger and thicker pipes tend to handle stress better, but they may also lead to heavier loads for supports.
Understanding these factors is crucial for effective stress analysis and design.
Benefits of Hiring a Professional Piping Stress Company
Many organizations choose to engage professional piping stress companies for detailed analysis. Here are some significant advantages:
Expertise in Compliance and Standards
Professional piping stress companies are well-versed with industry standards and codes such as ASME B31.3 and API 570. Compliance with these standards is critical for the design, analysis, and inspection of piping systems. Failure to comply can lead to severe penalties, operational delays, and increased risks. Skilled professionals ensure that all regulatory requirements are met, providing peace of mind and ensuring that systems are safe for use.
Improved Safety and System Integrity
By applying comprehensive stress analysis techniques, professionals can identify potential failure points within piping systems. This analysis typically includes examining factors like steady-state thermal expansion and seismic loads. With expertise, engineering firms can recommend design modifications or reinforcements that help mitigate risks and enhance the overall integrity of the piping infrastructure.
Cost-Effective Solutions for Complex Projects
Piping systems can be complex, with numerous variables impacting stress levels. Engaging with an experienced piping stress company can lead to more cost-effective solutions, especially in large-scale projects. Thorough analysis upfront can prevent costly redesigns or repairs during the construction or operational phases.
Analyzing Piping Loads and Responses
Understanding the loads that will act upon piping systems is key to effective stress analysis. This section discusses the different load types, their implications, and useful tools:
Differentiating Between Static and Dynamic Loads
Static loads are constant loads applied to a piping system. Examples include the weight of the pipe itself and static fluid weight. These loads don’t change over time. Dynamic loads, however, include variations due to external forces like wind, seismic activity, and the movement of fluids. Recognizing the difference is essential, as dynamic loads can lead to significantly increased stresses, requiring specific analysis techniques.
Common Load Scenarios in Piping Systems
Several load scenarios are essential to consider during stress analysis:
- Thermal Expansion: Changes in temperature cause pipes to expand and contract, which can induce stress if unaccounted for.
- Pressure Changes: Operating pressures can lead to increased stress levels within the piping system.
- Seismic Loads: Areas prone to earthquakes require additional analysis to ensure piping systems can withstand seismic ground movements.
Each of these scenarios demands thorough consideration to ensure piping systems remain functional and safe.
Tools and Software Used for Load Analysis
Modern piping stress analysis leverages software tools to simulate and analyze loads. Some of the most common tools include:
- CAESAR II: A widely used software solution for pipe stress analysis, which allows for the calculation of displacements and stresses from analysis models.
- AutoPIPE: An advanced program that provides capabilities for analyzing various piping configurations under diverse load scenarios.
- ROHR2: This software focuses on integrating piping and flexibility analysis, catering to advanced engineering needs.
Effectiveness of Software Tools
Using specialized software reduces manual calculation errors and improves efficiency in analysis, thereby allowing engineers to focus on optimizing design options and ensuring compliance with safety standards.
Best Practices for Pipe Stress Analysis
Maintaining the integrity of piping systems through optimal stress analysis involves adhering to best practices, including the following:
Implementing ASME and International Standards
Adhering to internationally recognized standards such as those specified by the American Society of Mechanical Engineers (ASME) enhances the quality and safety of piping systems. These standards offer guidelines on materials, design, construction, testing, and inspection protocols. Ensuring compliance improves not only safety but also operational reliability across various applications.
Regular Maintenance and Inspection Protocols
Routine inspections and maintenance should form part of any operational pipelay. Regular monitoring helps identify potential issues before they escalate into major failures. Consider the following:
- Conduct annual integrity assessments to evaluate the condition of piping systems.
- Implement a data-driven approach to monitor critical stress parameters.
- Use non-destructive testing techniques to reveal underlying issues without disrupting service.
Enforcing regular maintenance routines can significantly extend the lifespan of piping systems and contribute to uninterrupted operational efficiency.
Understanding the 1500 Rule for Stress Analysis
The “1500 rule” is an informal guideline used in the industry to assess whether detailed stress analysis is required. If the nominal pipe size multiplied by the temperature in Fahrenheit is below 1500, the piping may not require formal analysis. However, this is a general rule and various factors must be evaluated case-by-case to determine the necessity of a comprehensive analysis.
Future Trends in Piping Stress Solutions
As technology progresses, the field of piping stress analysis is set to evolve as well. Below are some emerging trends:
Integrating Smart Technology in Stress Analysis
Smart technology, such as the Internet of Things (IoT), is making its way into mechanical and piping engineering. Sensors can continuously monitor stress conditions in real-time, providing data that can be used for predictive maintenance and enabling quick responses to issues as they arise.
Environmental Considerations in Piping Design
With increasing global emphasis on environmental stewardship, piping design is being scrutinized for sustainability. This includes selecting eco-friendly materials and optimizing designs to minimize waste and emission while ensuring compliance with environmental regulations.
The Role of Advanced Software in Future Analysis
The future of piping stress analysis will likely see more comprehensive use of advanced software solutions that include artificial intelligence (AI) and machine learning (ML) capabilities. These technologies can predict potential stress issues using historical data patterns, optimizing the design and operational parameters of piping systems.