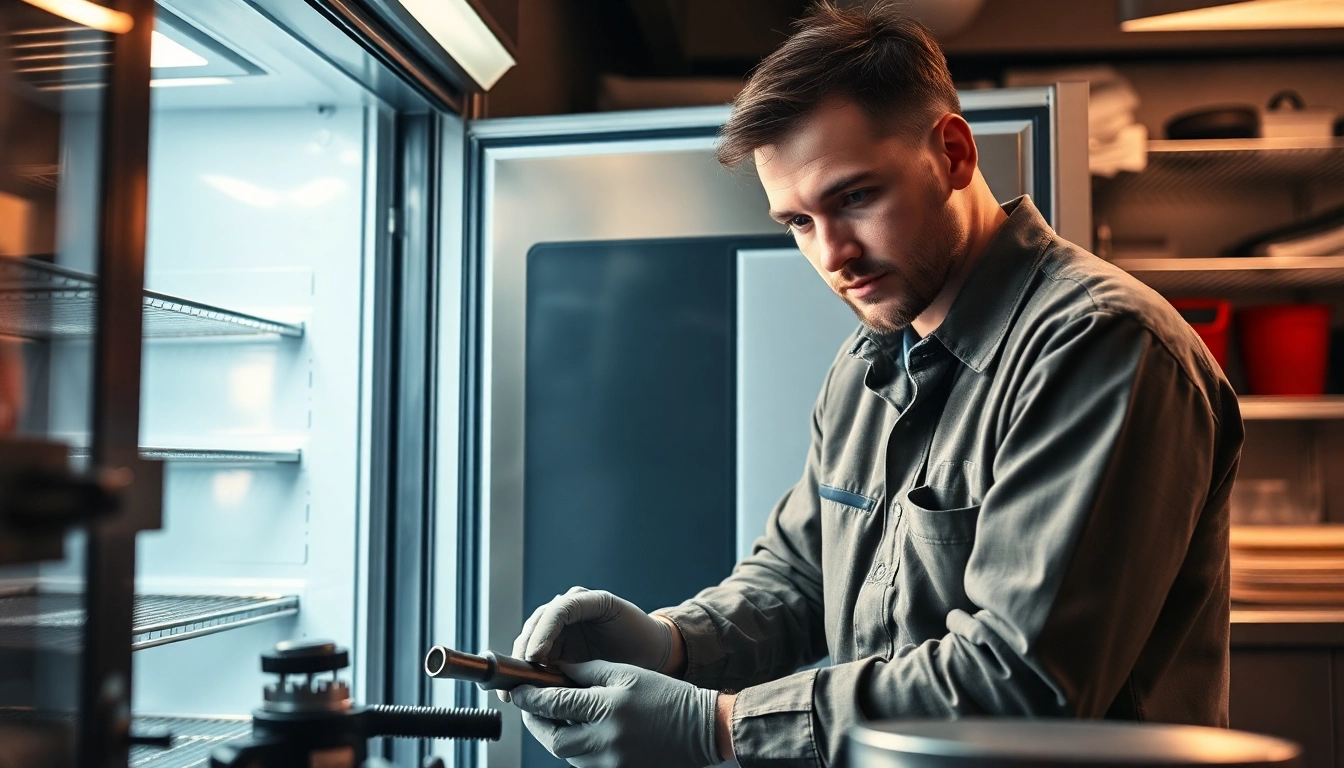
Understanding Walk in Freezer Repairs
Walk-in freezers are an essential component for many businesses, especially those in the food service, grocery, and healthcare sectors. They provide vital storage capabilities to keep products at safe temperatures, ensuring quality and safety for consumers. However, like any mechanical system, they are prone to wear and malfunction. Understanding the importance of walk in freezer repair is crucial for business continuity. Regular maintenance and timely repairs can extend the life of your unit and maintain operational efficiency. This article takes an in-depth look at walk in freezer repair, highlighting common issues, signs that indicate repair needs, and tips on selecting the right service provider.
Importance of Timely Repairs
Timely repairs to a walk-in freezer are critical for several reasons. First and foremost, failure to address issues promptly can lead to significant product loss. Any elevated temperature can lead to spoilage, particularly in food-related businesses, resulting in considerable financial loss. Furthermore, delayed repairs can cause more severe damage to the entire cooling system, raising repair costs exponentially.
Additionally, the operational downtime due to malfunctions can disrupt service to customers, negatively impacting your business reputation. Ensuring that your freezer is functioning optimally not only preserves your investments but also enhances customer satisfaction and retention.
Common Issues with Walk in Freezers
There are a variety of issues that can arise with walk-in freezers. The most common include:
- Temperature Fluctuations: Inconsistent temperatures can indicate problems with the thermostat or compressor, potentially leading to food spoilage.
- Frost Buildup: Excessive frost can restrict airflow, making it harder for the unit to maintain the right temperature.
- Water Leaks: Leaking water can result from clogged drain lines or damaged insulation, leading to potential structural damage and health hazards.
- Unusual Noises: Any strange sounds from the unit may indicate mechanical issues, such as worn-out bearings or loose parts.
Understanding these issues can help in diagnosing problems before they escalate into emergency repairs.
Benefits of Professional Service
Engaging a professional service for walk in freezer repair brings multiple advantages. Firstly, professionals have the training and experience necessary to accurately diagnose problems. Their tools and resources allow them to perform high-quality repairs efficiently. Additionally, they often offer warranties or guarantees, providing peace of mind that the repairs will hold up over time.
Professional services can also provide regular maintenance schedules, ensuring your walk-in freezer remains in good condition, thus prolonging its lifespan. They can keep your unit operating at peak efficiency, which is vital for energy savings in the long run.
Signs Your Walk in Freezer Needs Repair
Being aware of the signs that your walk-in freezer may need repair can help prevent costly damage and downtime. Here are a few indicators to watch for:
Temperature Fluctuations
If your walk-in freezer is experiencing temperature fluctuations, it could be a sign of an underlying issue. Consistent temperature is crucial for preserving food safety and quality. Check your thermostat settings; if it is set accordingly yet the temperatures vary, it may indicate compressor failure or problems with the refrigerant. Regular temperature monitoring is essential for any business relying on walk-in storage solutions.
Unusual Noises
Uncommon sounds such as grinding, screeching, or loud humming can indicate that mechanical parts are malfunctioning. These noises may come from the condenser fan, evaporator fan, or compressor. Ignoring these noises could lead to further complications that may require more extensive repairs. Listening closely can save time and costs in the long run.
Inefficient Performance
If your walk-in freezer takes longer than usual to cool down or maintain a set temperature, this inefficiency could result from several factors, including blocked air ducts, a malfunctioning condenser fan, or even dirty evaporator coils. Identifying and addressing these issues promptly can prevent larger problems from developing.
How to Select a Walk in Freezer Repair Service
Choosing the right repair service for your walk-in freezer is crucial for maintaining its efficiency and longevity. Below are key factors to consider when selecting a repair service:
Checking Credentials and Experience
Before hiring a repair technician, it’s essential to verify their credentials. Look for certifications, insurance, and any specialized training in refrigeration systems. An experienced technician will have a proven track record of solving similar problems. Industry standards vary, so make sure they are familiar with the specific model and type of your walk-in freezer.
Customer Reviews and Testimonials
Customer feedback is invaluable when assessing a service provider’s reliability. Look for reviews on various platforms, including Google and Yelp. Testimonials can provide insight into the quality of work, customer service, and reliability. Reputable companies often showcase their customer feedback on their websites as well.
Service Guarantees and Warranties
Understanding the warranties and guarantees offered by the service provider is essential. A satisfactory warranty on parts and labor can provide peace of mind that the repair work will be effective and reliable over time. It’s crucial to confirm the warranty details upfront to avoid conflicts later.
Cost Factors of Walk in Freezer Repair
The costs associated with walk-in freezer repairs can vary significantly based on several factors. Understanding these can help you budget effectively.
Understanding Repair vs. Replacement Costs
Deciding whether to repair or replace your walk-in freezer involves cost-benefit analysis. Generally, repairs are more economical if your unit is relatively new and the problems are not extensive. However, if your freezer is approaching the end of its lifespan (typically 10-15 years), investing in a new unit may be more practical. Repair costs can often range from $200 to $2,500, while new units can start at around $5,000 and go up considerably based on size and features.
Typical Repair Expenses
Several common repairs can impact costs, such as:
- Compressor Repair or Replacement: Costs range between $300 to $1,000 depending on the complexity.
- Thermostat Replacement: This could set you back $200 to $400.
- Evaporator Coil Cleaning: Typically costs around $100 to $300.
It’s wise to get an estimate before any work is done to avoid unexpected expenses.
Insurance and Warranty Considerations
Check if your business insurance covers equipment repairs. Many commercial insurance policies include electrical and mechanical failures as part of their coverage. Additionally, warranties on the unit or its components can alleviate some financial burdens regarding repairs. Always keep warranty documents accessible, as contractor service may require these for specific repairs.
DIY Maintenance Tips for Walk in Freezers
While professional repair services are essential for significant issues, regular DIY maintenance can prevent many problems and extend the lifespan of your walk-in freezer. Here are some effective practices:
Regular Cleaning Practices
Keeping the walk-in freezer clean is one of the easiest ways to maintain its functionality. Regularly cleaning the condenser coils and ensuring the drain pan is free of debris can significantly improve efficiency. It is also important to clean the door seals and ensure that they are intact, preventing warm air from entering the unit.
Monitoring Temperature Regularly
Implement a routine for checking the ambient temperatures of your walk-in freezer. Use high-quality temperature monitoring devices to receive alerts if the temperatures vary beyond acceptable levels. A dedicated monitoring system can help track performance over time and alert you to impending issues.
Preventing Common Issues
Adopt best practices to minimize common problems. Regularly inspecting the unit for signs of wear and tear can catch issues early. For example, ensure that there is no frost buildup in the freezer, as this can hamper airflow and affect temperature consistency. Preventive maintenance is often more cost-effective than emergency repairs and can help maintain optimal performance.