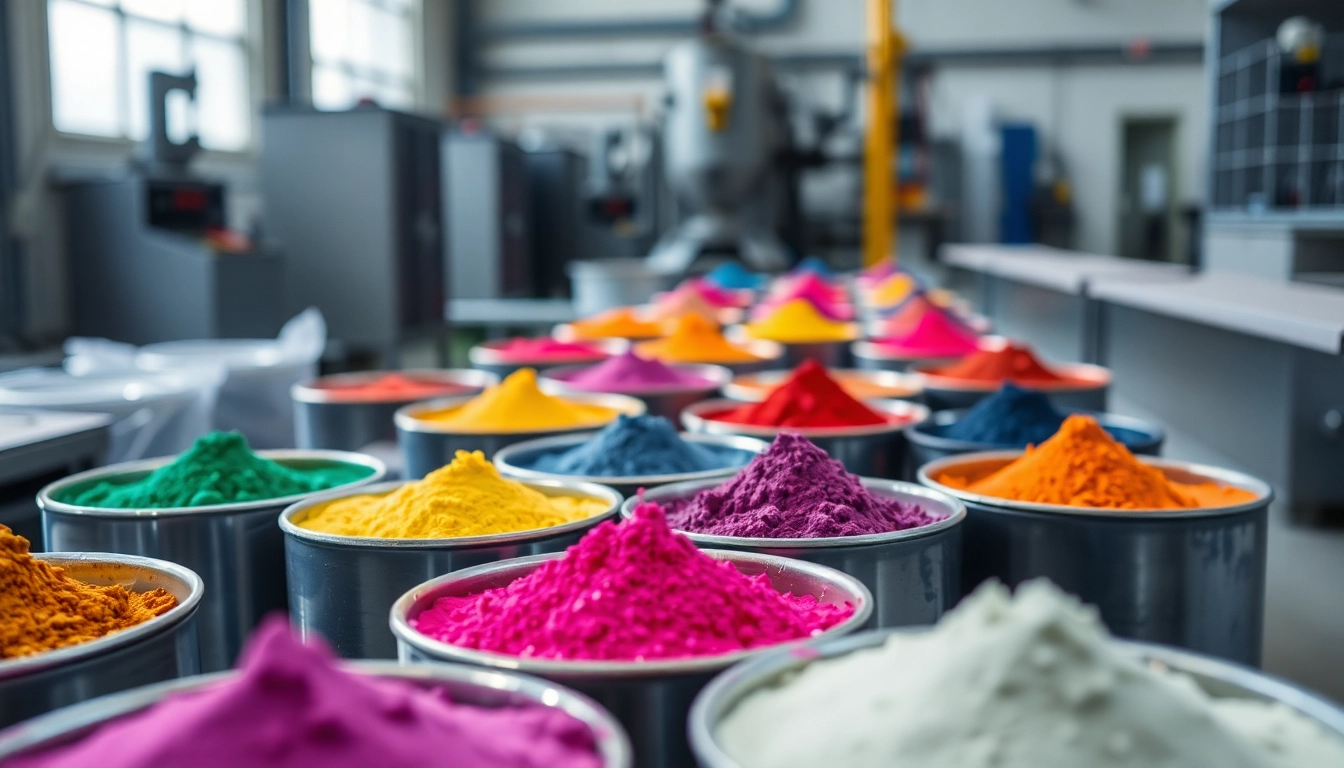
Understanding Powder Coating
In the manufacturing and finishing industries, powder coating has emerged as a preferred method for applying protective and aesthetic coatings to metal surfaces. Unlike traditional liquid paints, powder coating involves a dry finishing process that uses finely ground particles of pigment and resin, which are electrostatically charged and sprayed onto a surface. Once applied, the coated item is heated in an oven, where the powder melts and fuses into a protective layer. This unique process not only enhances durability but also provides a vibrant aesthetic finish. As a versatile solution, powder coating can be employed in various industries, leading to significant advancements in product longevity and quality.
What is Powder Coating?
Powder coating is a method of applying a decorative and protective finish to a wide array of materials, predominantly metals. It consists of a dry powder that contains resins, pigments, and additives. This mixture is applied electrostatically and cured under heat, creating a strong bond with the substrate material. The end result is a product that exhibits superior durability, enhanced resistance to scratching, chipping, fading, and wearing compared to conventional paint.
There are two primary types of powder coatings: thermosetting and thermoplastic. Thermosetting powders are chemically cured, creating a cross-linked structure that adds to their resilience. In contrast, thermoplastic powders can be reheated and reshaped without losing their integrity, making them suitable for specific applications.
The Powder Coating Process
The powder coating process consists of several key steps:
- Surface Preparation: The substrate must be thoroughly cleaned and prepped to remove any contaminants or previous coatings, ensuring optimal adhesion of the powder.
- Pretreatment: This may involve phosphating or chromating the surface, providing additional corrosion resistance and improving the bond.
- Application: Using an electrostatic spray gun, the powder is applied evenly to the surface. The electrical charge causes the powder particles to adhere to the metal surface.
- Curing: The coated item is placed in a curing oven where it is heated to a specific temperature, allowing the powder to melt and fuse into a solid coating.
- Cooling: After curing, the item is allowed to cool, solidifying the coating into a durable finish.
Key Benefits of Powder Coating
The advantages of powder coating are manifold, making it a popular choice for manufacturers and consumers alike:
- Durability: Powder coatings are highly resistant to impact, abrasion, and harsh weather conditions, significantly extending the lifespan of coated objects.
- Environmental Benefits: Unlike liquid paints, powder coatings emit zero or very low volatile organic compounds (VOCs), aligning with modern environmental regulations.
- Color Variety: A wide spectrum of colors and finishes, including textured and metallic options, allows for customizable aesthetics for varied applications.
- Chemical Resistance: Many powder coatings are resistant to chemicals and corrosive substances, making them suitable for industrial applications.
- Cost Effectiveness: The process can be more economical compared to traditional painting, especially for large batch productions, due to reduced material waste and increased efficiency.
Applications of Powder Coating
The versatility of powder coating allows it to be utilized across numerous industries and applications, ranging from automotive to household items.
Industries Utilizing Powder Coating
Many industries benefit from powder coating, including:
- Automotive: Powder coating enhances the durability and appearance of wheels, frames, and various automotive parts.
- Appliances: Household appliances such as refrigerators and washing machines often utilize powder coating for its durability and aesthetic value.
- Architecture: Architectural elements like window frames, railings, and metal siding are frequently powder coated for weather resistance and visual appeal.
- Furniture: Many modern furnishings employ powder coating to achieve stylish finishes that can withstand daily use.
- Sports Equipment: Equipment such as bicycles and gym apparatus benefit from the increased protection and color variety offered by powder coatings.
Common Products Coated with Powder
Numerous products are commonly powder coated, providing a blend of durability and aesthetics:
- Outdoor Furniture: Powder coating prevents rust and fading, making it ideal for outdoor use.
- Lighting Fixtures: Decorative lighting elements often feature powder coatings to enhance their aesthetic appeal and protect against corrosion.
- Automotive Parts: Various components, including bumpers and chassis, benefit from the protective qualities of powder coatings.
- Metal Fencing and Gates: These are coated to withstand environmental wear while maintaining visual appeal.
- Hardware: Door handles, knobs, and accessories can be powder coated for added durability and color options.
Innovative Uses of Powder Coating
Beyond traditional applications, powder coating has found innovative uses in specialized fields:
- Electronics: Conductive powder coatings are employed to enhance EMI shielding in electronic devices.
- Art and Design: Artists are using powder coating to create colorful sculptures and installations, showcasing the versatility of the medium.
- Medical Devices: In healthcare, powder coatings are used on equipment and instruments for their hygienic properties.
- Packaging: Some packaging materials are powder coated to improve durability and resistance to moisture and chemicals.
Powder Coating vs. Traditional Painting
When choosing a finishing technique, understanding the differences between powder coating and traditional paint can significantly influence project outcomes.
Durability and Performance Comparisons
Powder coating provides superior durability compared to traditional paints. The hardened finish from the curing process results in a coating that is highly resistant to scratches, chips, and other forms of damage. Traditional paint, while offering a range of colors and finishes, may not hold up as well under stress, weather, or UV exposure, leading to quicker degradation of the coated surface.
Cost-Effectiveness of Powder Coating
Cost analysis of both methods reveals that while the initial setup cost for powder coating might be higher (due to the required ovens and spray equipment), the long-term savings often outweigh this. Powder coating reduces waste and reapplication costs due to its durability. In contrast, traditional painting may incur additional expenses in terms of maintenance and reapplication over time.
Environmental Benefits of Powder Coating
Powder coatings are generally regarded as more environmentally friendly than traditional paints. They contain little to no VOCs, minimize air pollution, and reduce hazardous waste. This is a crucial consideration for modern manufacturing companies aiming to adhere to stringent environmental regulations.
Choosing the Right Powder Coating
Selection of the appropriate powder coating involves understanding available options and tailoring them to project requirements.
Types of Powder Coating Available
Different types of powder coatings can be chosen based on unique characteristics:
- Epoxy-based Powder Coatings: They offer excellent adhesion and corrosion resistance, making them ideal for indoor applications.
- Polyester Powder Coatings: Highly versatile, these are used for exterior applications due to their UV resistance and flexibility.
- Hybrid Powder Coatings: Combining properties of epoxy and polyester, hybrids balance durability and aesthetic appeal.
- Fluoropolymer Powder Coatings: These provide supreme chemical and UV resistance, perfect for highly demanding environments.
Color Selection and Custom Options
Powder coatings come in a vast array of colors and finishes. Custom color matching is also available for businesses looking to maintain brand identity. It is essential to consider factors such as gloss level, texture, and finish type when selecting colors to ensure optimal performance and appearance.
Factors to Consider When Selecting Powder Coatings
Several factors should be evaluated to make an informed choice:
- End Use: Consideration of where and how the finished product will be used informs the type of powder coating required.
- Environmental Conditions: UV resistance, moisture, and chemical exposure should dictate the choice of coating.
- Regulatory Compliance: Ensure that the selected powder complies with industry and environmental regulations.
- Application Method: Understanding the methods available for applying powder coatings can influence product selection.
Getting Started with Powder Coating
Starting a powder coating project can seem daunting, but with the right information and resources, it can be a rewarding endeavor.
DIY vs. Professional Powder Coating Services
The decision between DIY powder coating and hiring professionals depends on several factors including budget, skills, and the scale of the project. DIY kits are available for home use, providing a cost-effective way to coat small items. However, for larger projects or items requiring high-quality finishes, professional services may be more suitable. Professionals have access to commercial-grade equipment and ensure that the powder coating is applied evenly and cured correctly.
Essential Equipment for Powder Coating
Those considering DIY powder coating will need specific equipment, including:
- Powder Coating Gun: This device applies the powder evenly and is crucial for successful coating.
- Curing Oven: Essential for melting and curing the powder into a solid finish.
- Sanding and Cleaning Supplies: To prepare surfaces adequately for coating.
- Safety Gear: Protective clothing, respirators, and gloves to ensure safety during the application process.
Tips for Successful Powder Coating Projects
To ensure a successful powder coating project, consider the following tips:
- Proper Preparation: Thoroughly clean and prep surfaces to remove grease, dust, or old coatings to facilitate optimal adhesion.
- Test Small Areas: Before committing to a large batch, test the powder coating on a small item to assess color and texture.
- Follow Manufacturer Guidelines: Adhere to the specific application and curing instructions provided for the powder coating used.
- Monitor Cure Times: Ensure proper curing times and temperatures to guarantee the durability of the finish.